Rotational Molding
Overview of Rotomolding Services
With the use of rotational molding services, hollow yet durable parts can be manufactured at reasonable tooling costs. At Holmes Gustafson & Associates, LLC we can provide assistance with tooling and fixture design, material selection, and can customize the design and engineering process to ensure the best-case development of your product.
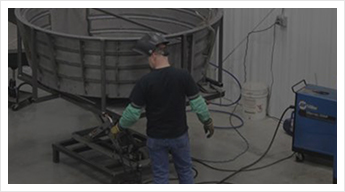
We work with Horizon Manufacturing Group, LLC to provide rotational molding to 107”, including in-house foaming & tooling, custom design and color, and other value-added services. There are also various secondary finishing options available along with specialized assembly.
Polyethylene is a common material for rotational molding, but other resins can also be used (including nylon). Horizon offers waste container lids and liners in Polyethylene as well as FDA and NSF approved flame-retardant materials.
Below are some of the advantages and disadvantages of using rotational molding:
Advantages: (the right process for many parts)
- Suitable for low-volume production
- Ideal for hollow shapes
- Simple process
- Allows for cost-effective production of large components
- Less expensive to set up and operate than injection molding
- Low cost of parts
- Highly adaptable from batch production to high-volume mass-production
Disadvantages: (not an optimal process for every condition)
- Not ideal for making small, precise components
- Compared to other plastic molding methods, tolerances are low
- Cycle times can be longer when compared with other plastic molding methods
Contact Holmes-Gustafson & Associates at (815) 985-5116 and let us advise you on the best process for your desired parts!